Agile, DevOps, TPS, TOC, Deming’s System of Profound Knowledge, and Lean. Is there a mental construct or latticework that connects these robust systems? I believe the answer can be found in Wiring the Winning Organization. The authors Gene Kim and Steve Spear introduce the concepts of the three layers of work and social circuitry. The book also explains its three biggest learning pillars: simplification, slowification, and amplification.
Interview Highlights
- Three approaches to reading this book.
- The circuitry analogy is brilliant.
- Not a replacement for #DevOps, TPS. Lean, or TOC.
- The Three Layers of Work.
- Slowification – a simple definition
- Coach Charlie Francis and slowing down the game.
- Simplification – three techniques and the Skinner research
- Amplification – the Southwest story.
- Next steps – how do we teach these concepts to the rest of the team?
- A shoutout to the book’s illustrators.
Wiring the Winning Organization: Amazon | Audible
Book Club Questions
I mentioned this would be great book club material during the conversation with Gene Kim and Steve Spears.
Below are questions to consider should you find a small group to discuss this book with:
- Gene and Steve discuss circuitry. What happens when faulty circuitry exists in the department, a team, or an organization?
- The three layers of work are a great refresher on the holistic nature of getting work done. Do a Google search on Brian Joyner and his leadership triangle. How do these mental models compare, and how can you use both in your work?
- Is the social layer the weakest link in your organization? Why?
- In your own words, explain Slowification, Simplification, and Amplification. If you were teaching a workshop in your organization, how would you teach these concepts to make them sticky and usable?
- How do divergent and convergent thinking apply to these critical pillars?
- Planning, practice, and performance. Is practice lacking in your organization? If so, what are some good ideas for improvement?
- The Nummi story is one of my favorites in the book. How did the Toyota management team use Slowify, Simplify, and Amplify in this plant? Remember, absenteeism was once 20% at this plant. GM finally shut this plant down. One year after production resumed between the Toyota-GM joint venture, Nummi had the highest quality and productivity of any GM plant. How?
Bonus Question:
Who was Norman Bodek, and what can we learn from him? For further study, consider reading The Harada Method: The Spirit of Self-Reliance.
Important Links
- IT Revolution publisher sales page
- Gene Kim’s LinkedIn profile
- Steve Spear’s LinkedIn profile
Additional resources provided by Steve Spear:
- The book’s forward and Part I
- Chapters 1 and 9 of The High-Velocity Edge
- See to Solve LinkedIn profile page and their website
- The Northeast Lean Conference and their LinkedIn profile page
- MIT Sloan Executive Education on High-Velocity Organizations
Episode Pairings
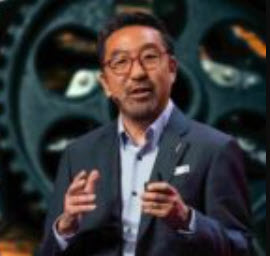
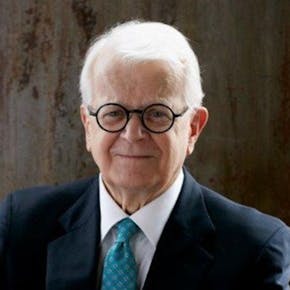
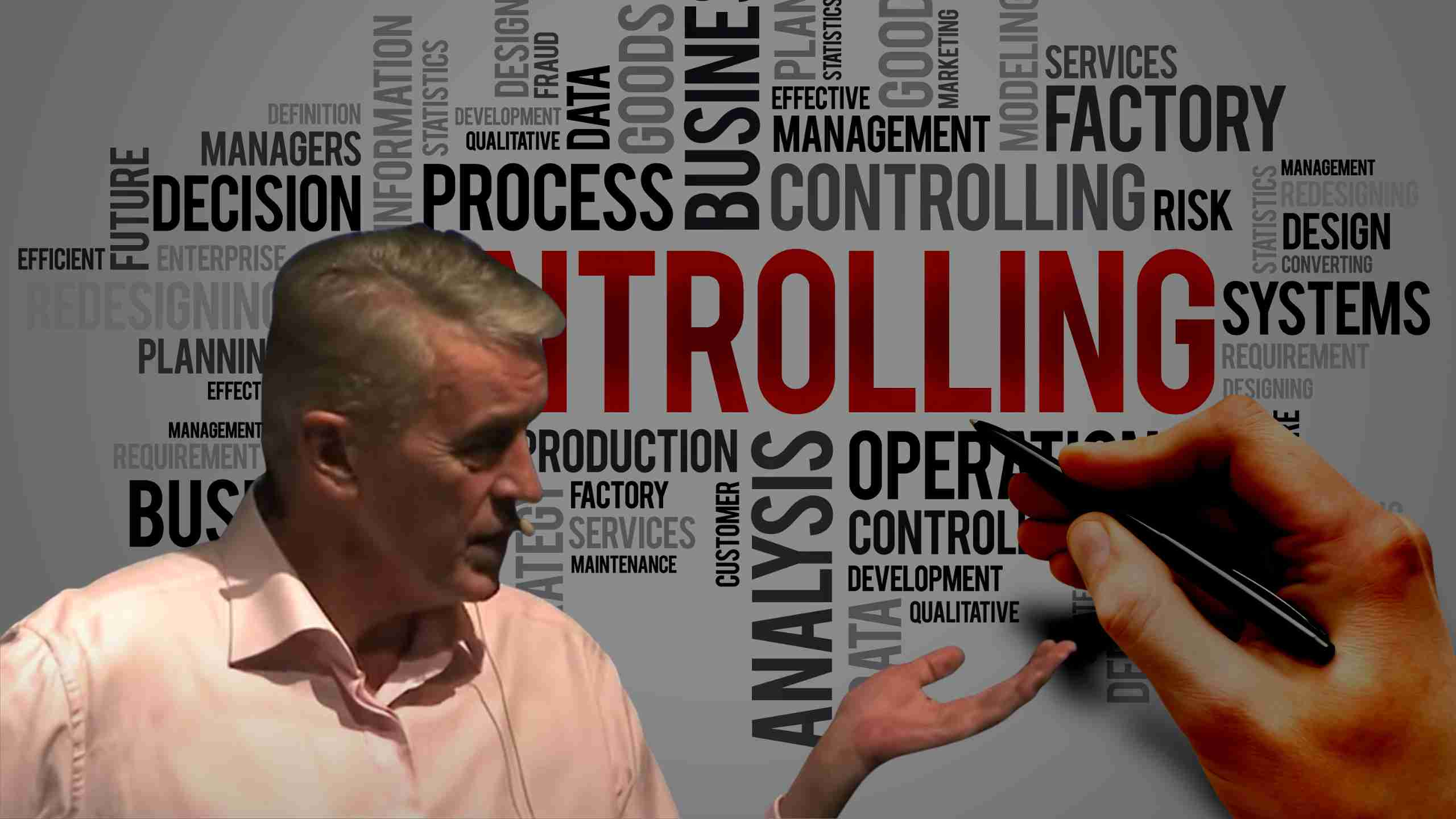
Leave a Reply